Ever wondered what goes on behind the scenes of those sleek batteries powering your electric vehicle? The battery manufacturing process steps represent an intricate dance of chemistry, engineering, and precision that transforms raw materials into powerful energy storage devices. While most of us appreciate the end result—a car that whispers down the highway with zero emissions—few understand the complex journey these power cells undergo before reaching your vehicle.
Today, we’re pulling back the curtain on the fascinating world of modern battery production. Grab a cup of coffee and join me as we journey through the high-tech facilities where tomorrow’s energy storage solutions are born!
The Symphony of Battery Production
Creating a lithium-ion battery isn’t just assembly line work—it’s more like conducting an orchestra where every instrument must play perfectly in time. One false note (or in this case, one microscopic contaminant) can ruin the entire performance.
1. Electrode Manufacturing Process: Where It All Begins
The electrode manufacturing process is foundational to battery performance. Every step here directly impacts the final product’s capacity, charge rate, and lifespan.
1.1 Slurry Preparation: The Battery’s Secret Sauce
The first movement in our battery symphony begins with something that looks surprisingly like cake batter—a carefully formulated slurry. This mixture combines active materials (the real workhorses of energy storage) with binders that hold everything together.
For cathodes (the positive electrode), manufacturers typically use lithium-metal oxides mixed with PVDF (polyvinylidene fluoride) binders and solvents like NMP (N-Methyl-2-pyrrolidone). The anode (negative electrode) slurry usually contains graphite as its active material.
Here’s where it gets interesting: these mixtures must be stirred in vacuum conditions to eliminate air bubbles. It might seem like a small detail, but those tiny air pockets can significantly reduce energy density optimization potential. For batteries pushing beyond 250 Wh/kg (the gold standard for modern EVs), this step is absolutely critical.
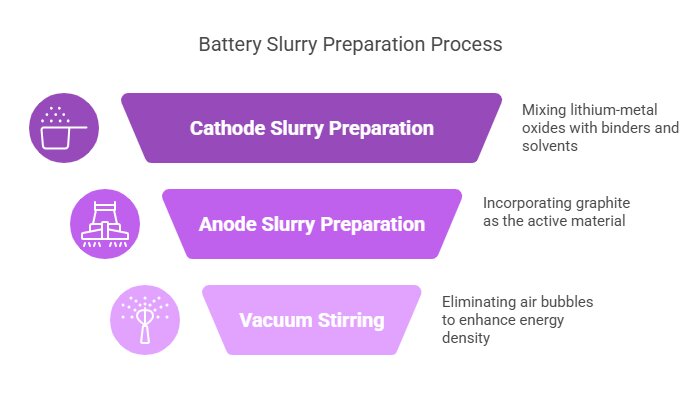
1.2 Cathode/Anode Coating Techniques: Precision in Motion
With our slurries prepared, it’s time to apply them to metal foil backings called current collectors. Think of this like spreading frosting on a cake—except this frosting needs to be applied with micrometer precision.
Modern cathode/anode coating techniques employ slot-die coating machines that apply the slurry in perfectly even layers:
- Cathode materials coat aluminum foil
- Anode materials coat copper foil
After coating, these wet electrodes take a long journey (up to 80 meters!) through drying ovens operating at 120–150°C. This process evaporates the solvents, leaving behind just the active materials bonded to the foil.
1.3 Calendering: The Great Compression
Next up, our electrodes need to be compressed to just the right density. This happens through a process called calendering, where the coated foils pass through massive rollers (exerting up to 10 tons of pressure) that compress the coating to around 3.5–4.0 g/cm³.
This compression isn’t just about making the electrode thinner—it actually enhances ionic conductivity by 15–20% by reducing the gaps between particles. Better conductivity means faster charging and better performance!

1.4 Slitting & Notching: Cutting to Size
Our electrodes are now ready to be cut to their final dimensions. For example, if we’re making 21700 cylindrical cells (a format popularized by Tesla), we’ll cut the electrodes to about 80mm width.
Precision lasers then create notches or tabs on these electrodes—these will later serve as connection points for the battery’s terminals. Proper current collector alignment during this phase is crucial, as even minor misalignments can lead to capacity loss or even safety issues down the line.
2. Cell Assembly Automation: Bringing Components Together
Modern lithium-ion battery production lines rely heavily on cell assembly automation to ensure consistency and precision at speeds that would be impossible with manual processes.
2.1 Stacking/Winding: Architecture Matters
Depending on the battery design, the prepared electrodes now either get stacked (for prismatic and pouch cells) or wound (for cylindrical cells).
Pouch cells use what’s called Z-fold stacking with a flexible polymer-coated aluminum casing. If you’ve seen the flat batteries in many modern EVs, those are likely pouch cells.
Cylindrical cells, like Tesla’s innovative 4680 format, involve winding the layers into a “jelly roll” before inserting them into steel cans. This cylindrical design offers excellent mechanical stability—important when you’re accelerating a two-ton vehicle!
2.2 Separator Integration: The Peacekeeper
Between each layer of cathode and anode lies an unsung hero of battery safety—the separator. These thin (just 16–20µm) ceramic-coated polyethylene films have a crucial job: allowing lithium ions to pass through while preventing the electrodes from touching and causing a short circuit.
Modern separators also help prevent dendrite growth—tiny lithium “trees” that can eventually puncture the separator and cause catastrophic failure. No pressure, little separator film!
2.3 Electrolyte Filling: The Magic Fluid
Now comes the liquid that makes everything work—the electrolyte. Typically consisting of lithium hexafluorophosphate (LiPF₆) dissolved in a mixture of ethylene carbonate and dimethyl carbonate, this fluid enables lithium ions to shuttle between electrodes.
This filling process occurs under vacuum conditions, with approximately 0.5–1.0 grams of electrolyte used per ampere-hour of battery capacity. And here’s a fun fact about dry room requirements for battery production: these facilities maintain moisture levels below 20 parts per million—drier than many deserts on Earth! Workers in these hyper-dry environments sometimes even get nosebleeds from the extreme lack of humidity.
2.4 Sealing: Locking It All In
With all components in place, it’s time to seal the cell. For prismatic cells, manufacturers use 1,064nm fiber lasers to create hermetic seals. Pouch cells undergo heat sealing at 180–200°C.
This sealing must be perfect—any microscopic leakage path could allow moisture in or electrolyte out, both scenarios spelling disaster for battery performance and safety.
3. Formation & Conditioning: Waking Up the Battery
3.1 Initial Charging: The First Breath
Now comes a fascinating transformation—the first charge. This initial charging process, done at a very slow rate (0.1C, meaning it takes about 10 hours), forms what’s called the solid electrolyte interphase (SEI) formation layer on the anode.
This 50–100 nanometer-thick layer might seem insignificant, but it’s absolutely crucial for battery longevity. Think of it as the battery’s protective skin, preventing continuous reactions between the electrolyte and anode that would otherwise degrade the battery.
Battery formation chamber design is critical here—these specialized chambers precisely control temperature and voltage during this delicate process. During formation, voltage is monitored with extraordinary precision—to within ±2 millivolts. Any deviation could indicate internal problems requiring intervention.
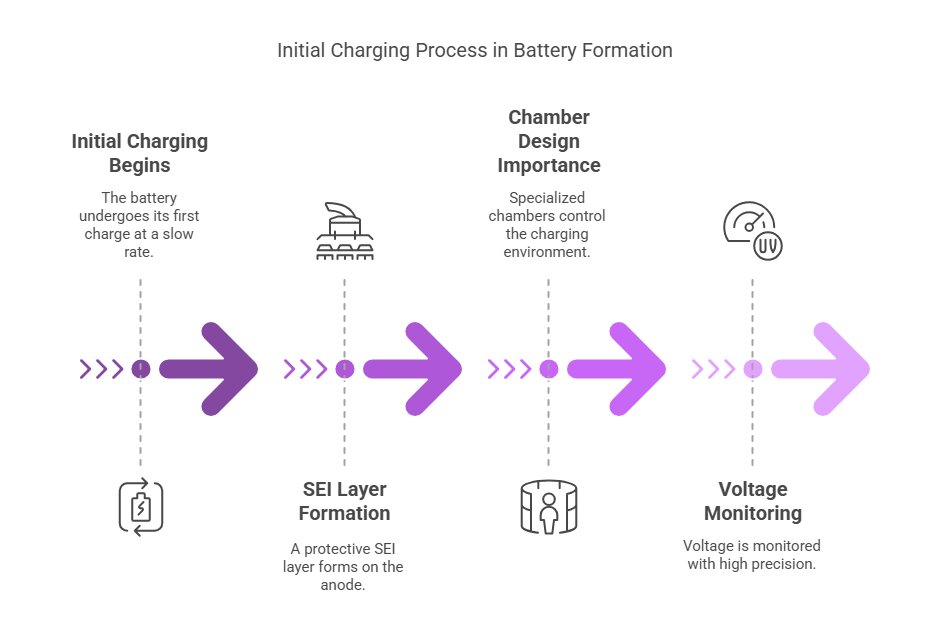
3.2 Aging: The Patience Game
After formation, batteries enter an aging period—typically 14–21 days at elevated temperatures (around 45°C). This might seem counterintuitive (aren’t high temperatures bad for batteries?), but this controlled aging helps stabilize the internal chemistry.
After this process, capacity variance between cells should be no more than 2%—important when you’re connecting hundreds of cells together in an EV battery pack.
3.3 Grading: Only the Best Make the Cut
Modern battery factories employ AI-powered systems to grade cells by capacity (with variances of just ±0.5%) and internal impedance. Cells with similar characteristics are grouped together to ensure optimal performance when assembled into modules and packs.
4. Module/Pack Assembly: Building the Power System
4.1 Module Integration: Strength in Numbers
Individual cells are now connected together to form modules. Ultrasonic welding in battery tabs is the preferred method for creating these connections. This technique uses high-frequency (20kHz) vibrations to join metals without excessive heat, creating strong electrical connections without damaging the sensitive components inside.
For EVs, liquid cooling plates are integrated between cells or modules. Tesla’s glycol-based cooling systems, for example, help maintain optimal temperature across the entire battery pack—essential for both performance and longevity.
4.2 BMS Integration: The Battery’s Brain
No modern battery pack is complete without its brain—the Battery Management System (BMS). This sophisticated electronic system monitors:
- Cell balancing (keeping voltage differences between cells within ±10mV)
- Temperature gradients (ideally less than 5°C across the pack)
- Charge/discharge rates
- Overall pack health
The BMS is the unsung hero that prevents your EV battery from overcharging, overheating, or operating outside its safe parameters.
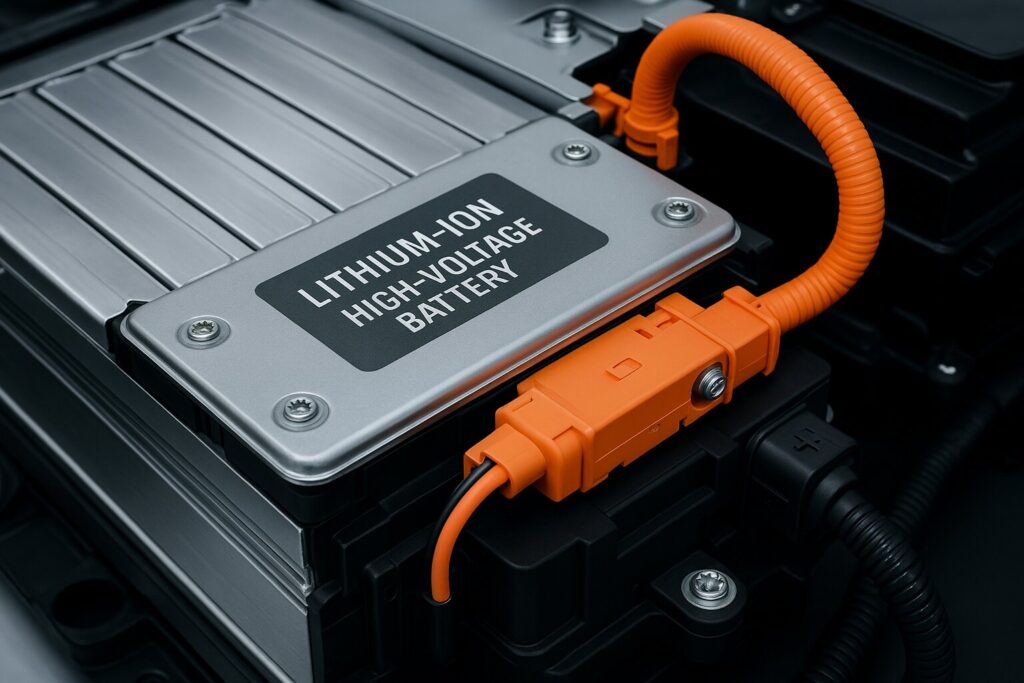
5. Quality Control in Battery Manufacturing: Trust, but Verify
5.1 X-Ray Inspection: Seeing the Invisible
Quality control in battery manufacturing is rigorous and multi-layered. Before batteries leave the factory, they undergo thorough inspection. X-ray systems can detect microscopic defects (down to 50µm) that might cause short circuits or other failures. This non-destructive testing allows manufacturers to catch potential issues before batteries reach consumers.
5.2 Thermal Runway Testing: Safety First
Sample cells from each production batch undergo rigorous safety testing, including thermal runway tests where cells are gradually heated until failure (typically occurring above 130°C). These tests help ensure that even in worst-case scenarios, batteries will fail safely rather than catastrophically.
5.3 Cycle Life Validation: Built to Last
Finally, sample cells undergo accelerated cycling—1,000+ charge-discharge cycles at 1C rate—to ensure they maintain at least 80% of their original capacity. This simulates years of real-world use in just weeks, helping manufacturers guarantee battery longevity.
The Cutting Edge: Innovation Never Stops
The battery industry isn’t standing still. Exciting innovations continue to push performance boundaries:
- LG Energy Solution‘s DLD (Direct Lamination Design) Coating enables simultaneous dual-layer electrode coating, boosting production efficiency.
- CATL’s Cell-to-Pack (CTP) technology eliminates module housings, increasing energy density by about 10%.
- Tesla’s dry electrode technology eliminates solvents altogether, reducing energy consumption in manufacturing by a remarkable 70%.
With electric vehicle adoption accelerating worldwide, advances in lithium-ion battery production lines will continue to make batteries more energy-dense, longer-lasting, and more affordable.
Conclusion: The Future Is Electric
From slurry mixing to final testing, modern battery production represents the perfect marriage of chemistry, precision engineering, and advanced manufacturing. The humble battery—once a simple device for starting cars or powering flashlights—has evolved into a technological marvel enabling the transition away from fossil fuels.
Next time you silently accelerate in your EV, spare a thought for the incredible journey those batteries took before they found their home under your feet. The road to a cleaner future is paved with innovations in energy storage—and this is just the beginning.
What aspects of battery manufacturing fascinate you most? Are there other battery technologies you’d like to learn about? Share your thoughts in the comments below!
Frequently Asked Questions
1. What are the 7 essential steps in lithium battery manufacturing?
The complete process follows a precise sequence: Mixing (combining active materials with binders) → Coating (applying slurries to metal foils) → Calendering (compressing electrodes) → Slitting (cutting to size) → Cell Assembly (combining components) → Formation (initial charging to create protective layers) → Testing (quality assurance).
2. What raw materials are critical for battery electrode production?
Key materials include lithium compounds (providing the essential ions), graphite anodes (hosting lithium during charging), nickel/cobalt cathodes (determining energy density), and aluminum/copper foils (serving as current collectors for cathodes and anodes respectively).
3. How does quality control ensure battery safety?
Safety relies on multiple testing methods: X-ray inspection detects internal defects, thermal runaway testing verifies safe failure modes, impedance measurement identifies internal resistance issues, and cycle life validation confirms long-term stability and performance.
4. What’s the difference between anode vs. cathode manufacturing?
Anodes use copper foil + graphite for excellent conductivity and lithium storage, while cathodes use aluminum foil + metal oxides (containing nickel, cobalt, manganese, or aluminum) that determine many performance characteristics. Cathode manufacturing typically requires higher precision due to more complex chemistry.
5. Why is the formation process crucial?
Formation creates the protective SEI layer on the anode, activates proper electrochemical pathways, and prevents early degradation by establishing stable interfaces. Without proper formation, batteries would experience rapid capacity fade and potential safety issues.
6. What equipment is needed for battery module assembly?
Essential equipment includes laser welders for electrical connections, stacking machines for cell arrangement, glove boxes for controlled environments, and electrolyte filling systems for precise metering under vacuum conditions.
7. How long does full production take from start to finish?
The complete process spans 14-21 days on average. While manufacturing steps take only 2-3 days, formation charging (10-12 hours) and critical aging processes (1-2 weeks) cannot be rushed without compromising quality and longevity.
8. What environmental regulations apply to battery plants?
Key regulations mandate solvent recovery systems to capture and recycle chemicals, water treatment protocols for handling metal-contaminated water, and recycling compliance for production scrap containing valuable metals like cobalt and nickel.
9. What causes battery defects during manufacturing?
Common issues include moisture contamination (even at parts-per-million levels), coating irregularities creating uneven current distribution, tab welding failures resulting in high-resistance connections, and separator misalignment leading to potential short circuits.
10. How do production costs break down per kWh?
Typical cost breakdown: 40% materials (with cathode materials being the largest portion), 25% labor (varying by region and automation level), 20% equipment (including specialized machinery and facilities), and 15% for testing/QA procedures ensuring safety and performance.
Want to Learn More About EV Batteries?
Still have questions about EV battery lifespan, charging best practices, and battery replacement? Check out our EV Battery FAQ Page for expert answers to the most common questions!